The Scientific Research Behind Porosity: A Comprehensive Overview for Welders and Fabricators
Understanding the detailed systems behind porosity in welding is crucial for welders and makers striving for remarkable workmanship. As metalworkers look into the depths of this phenomenon, they uncover a world regulated by numerous factors that affect the development of these minuscule gaps within welds. From the composition of the base products to the ins and outs of the welding process itself, a wide range of variables conspire to either exacerbate or minimize the existence of porosity. In this extensive overview, we will certainly untangle the scientific research behind porosity, exploring its effects on weld high quality and unveiling progressed strategies for its control. Join us on this journey with the microcosm of welding blemishes, where precision fulfills understanding in the pursuit of flawless welds.
Understanding Porosity in Welding
FIRST SENTENCE:
Examination of porosity in welding exposes vital insights into the honesty and top quality of the weld joint. Porosity, characterized by the existence of tooth cavities or spaces within the weld metal, is a typical concern in welding processes. These voids, if not effectively dealt with, can jeopardize the architectural honesty and mechanical properties of the weld, bring about prospective failings in the ended up product.

To identify and measure porosity, non-destructive screening approaches such as ultrasonic testing or X-ray examination are frequently used. These methods enable for the identification of interior problems without jeopardizing the stability of the weld. By assessing the dimension, shape, and distribution of porosity within a weld, welders can make informed decisions to boost their welding procedures and attain sounder weld joints.
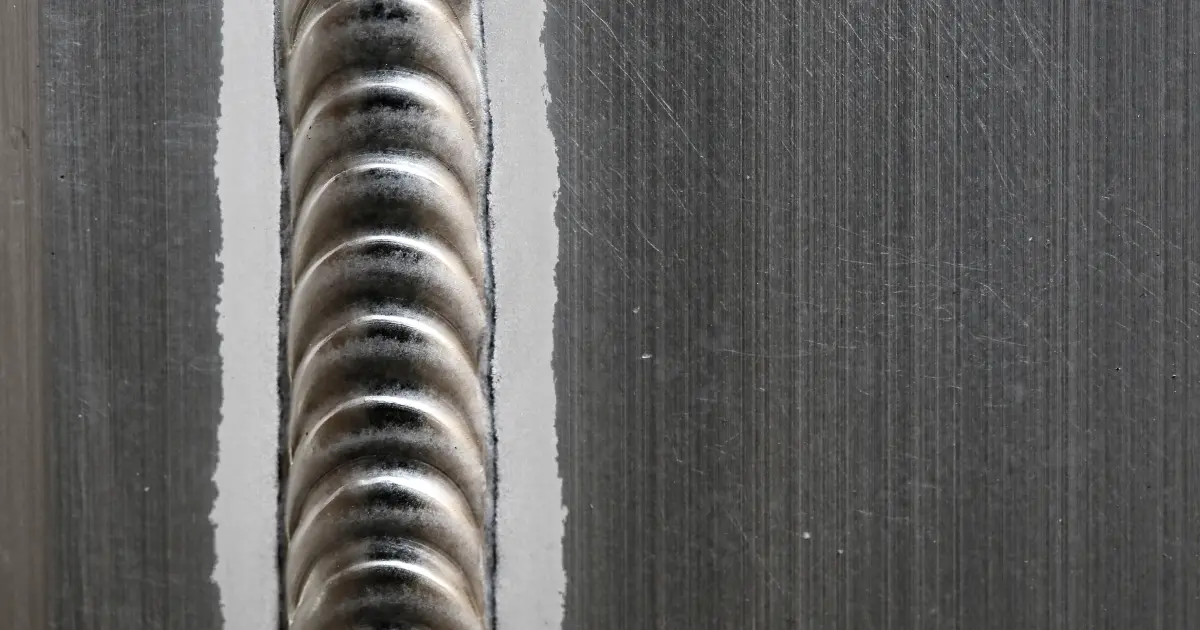
Variables Affecting Porosity Development
The event of porosity in welding is influenced by a myriad of aspects, varying from gas securing effectiveness to the details of welding criterion settings. Welding criteria, including voltage, current, take a trip rate, and electrode type, also effect porosity formation. The welding method utilized, such as gas metal arc welding (GMAW) or protected metal arc welding (SMAW), can affect porosity development due to variants in warm circulation and gas protection - What is Porosity.
Impacts of Porosity on Weld Top Quality
The visibility of porosity additionally compromises the weld's resistance important link to rust, as the caught air or gases within the gaps can react with the surrounding setting, leading to destruction over time. In addition, porosity can impede the weld's capacity to hold up against stress or influence, more endangering the overall quality and dependability of the welded structure. In essential applications such as aerospace, automotive, or architectural building and constructions, where safety and durability are paramount, the detrimental results of porosity on weld top quality can have extreme consequences, emphasizing the importance of decreasing porosity via proper welding methods and procedures.
Strategies to Lessen Porosity
In addition, making use of the ideal welding parameters, such as the correct voltage, existing, and take a trip speed, is vital in preventing porosity. Preserving a consistent arc length and angle during welding additionally assists minimize the possibility of porosity.

Additionally, picking the ideal shielding gas and maintaining appropriate gas circulation rates are crucial in minimizing porosity. Making use of the appropriate welding technique, such as back-stepping or using a weaving movement, can additionally help distribute warm evenly and decrease the opportunities of porosity formation. Finally, making certain correct ventilation in the welding atmosphere to eliminate any prospective resources of contamination is crucial for accomplishing porosity-free welds. By executing these techniques, welders can successfully lessen porosity and generate top quality bonded joints.
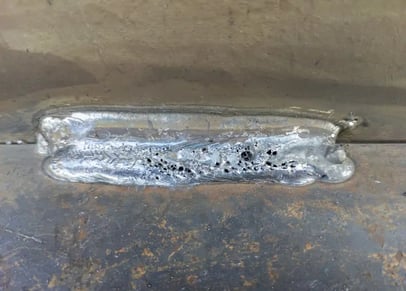
Advanced Solutions for Porosity Control
Implementing advanced innovations and ingenious approaches plays a crucial role in achieving exceptional control over porosity in welding processes. Additionally, employing innovative welding methods such as pulsed MIG welding or customized ambience welding can additionally assist minimize porosity problems.
An additional advanced service involves the use of advanced welding devices. Using devices with built-in functions like waveform control and advanced power sources can enhance weld official website quality and minimize porosity threats. The application of automated welding systems with specific control over parameters can substantially minimize porosity problems.
Additionally, incorporating sophisticated tracking and inspection modern technologies such as real-time X-ray imaging or automated ultrasonic screening can aid in detecting porosity early in the welding procedure, permitting immediate rehabilitative actions. Generally, incorporating these advanced options can substantially enhance porosity control and boost the total quality of welded parts.
Conclusion
In conclusion, recognizing the science behind porosity in welding is crucial for welders and fabricators to generate high-grade welds - What is Porosity. Advanced options for porosity control can special info even more enhance the welding process and guarantee a solid and dependable weld.